I think I have established that I have an
unhealthy fascination with the Sturmey Archer GH6 dynohub. The hub has an output of about 1.8W, although doing a little experimenting with my
digital buck converter on my
dynamo testing jig, it appears that the hub reaches its saturation current at considerably higher speeds than contemporary hub dynamos (at least in my test setup with a 1966 GH6). If the point of the buck converter is to extract more power out of the hub, there's not much practical use if that power isn't available until you're going 40 km/h!
 |
Speed versus current of a GH6 powering two series LEDs through a digital buck converter at 100% and 50% pulse width duty cycle. Error bars are standard deviation from the mean of 4 readings taken at each speed. |
The GH6 is old technology and seems primarily limited by the fact that it has a rather weak 20 pole
Alnico magnet, which is reported to lose a significant amount of flux over time. The few GH6 experts out there maintain that if a Dynohub has been serviced there is a good chance that the mechanic
damaged the magnet by removing the armature. Amazingly, Jobst Brandt, of
The Bicycle Wheel fame, built a
re-magnetizing device (very bottom of page) to refurbish the magnet in the event of the hub being disassembled improperly.
 |
GH6 20 pole manget (GL343) and armature (GL603) |
I
wondered if it would be possible to upgrade the magnet with modern
Neodymium magnets. After some more searching I discovered that I wasn't the only one that had thought of this. Ben over at
gotwind.org tried a couple of configurations and got something that
worked, although not well enough for his application. His results are promising for my application though as he reports getting higher voltage due to the increased flux of the new magnets and perhaps even a higher saturation current.
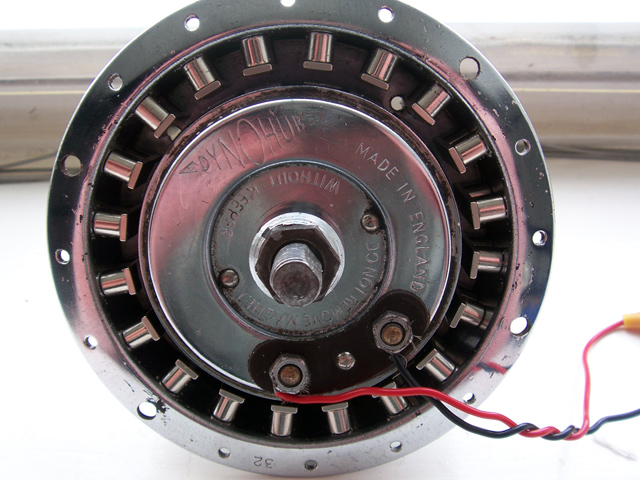 |
Ben@gotwind.org replaced the 20 pole Alnico ring magnet with 20 neodymium magnets in a GH6 hub |
Based on Ben's description, a magnet upgrade to the GH6 might be able to bring it up to spec with modern hub dynamos (rated voltage at low speeds, saturation current around 0.5A), albeit with more drag and probably lower efficiency. After some pondering and a bit more research, I think I'm going to have a go at making an adapter to fit the GH6 with 20 new Neodymium magnets. One planned improvement over Ben's efforts will be to keep the spacing between the stator and the magnets as close to the original specs as possible. The actually spacing is probably in the order of 0.010 to 0.020". I'm aiming for around 0.050", whereas Ben's design is reported to have 3mm (0.118") spacing. The trick will be to pick magnets of appropriate strength that are strong enough to saturate the stator at low speeds, but not so strong that they add undesirable
cogging effects and drag. Thus far, I have a design I'm shopping around to machinists:
 |
Proposed magnet adapter with armature |
 |
3D view of proposed GH6 magnet adapter |
Not sure yet what material it should be made of. At first, I thought of using ferromagnetic steel so the magnets would stick to it. This is more expensive and heavier than using 6061 aluminum, which might be a better solution as the longer I consider it the more I realize that whatever the material, I'll need to epoxy the magnets in place.
So, fingers crossed that these efforts will result in a GH6 with improved lower speed performance!
Update: magnets arrived today and, boy, are they strong! It's been said that Nd magnets are 10 times stronger than Alnico magnets. Now that I have some in hand I believe it. As stated previously, I think the challenge will be to use a magnet that is just strong enough to saturate the stator but not so strong that it adds additional drag due to
cogging torque.